Material handling equipment: check these best practices to use them
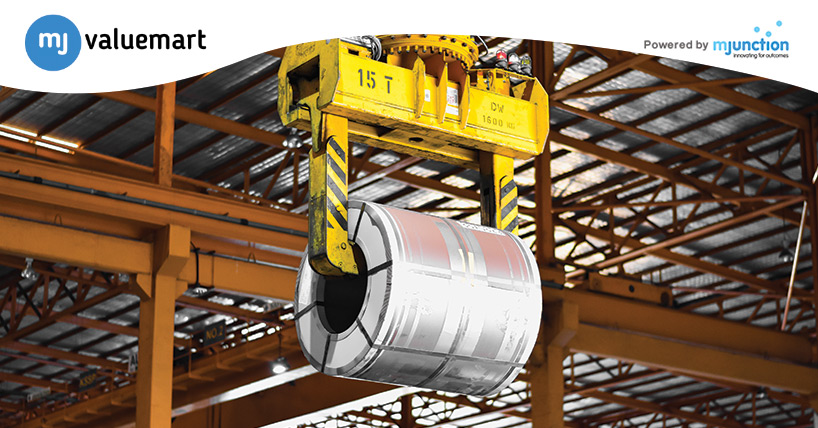
A material handling equipment is any mechanical equipment, which is used for storing and controlling products and goods. It is used in every stage of a product's lifecycle, from manufacturing to disposal. For example, forklifts can lift and move heavy stuff easily and conveyor belts carry items from one place to another. The proper use of these equipment not only ensures smooth operations but also contributes to workplace safety and productivity. Here we discuss some of the best practices to maintain when dealing with such equipment -
1. Selecting a material handling equipment that perfectly matches the unique needs of specific tasks, for instance, lift capacity, reach, or speed, guarantees seamless and efficient movement of materials. Moreover, the design that maximises the use of available space can boost storage capabilities and enhance the flow of operations. Modern selection and design of these equipment considers the integration with cutting-edge technology, such as automation, the Internet of Things (IoT), or data analytics to elevate operational efficiency, enable real-time monitoring, and facilitate data-driven decision-making.
2. Efficiently managing the load on these equipment is crucial - as it can minimise accident risk, damage to the equipment and to the products it is handling. Apart from the right amount of load, another thing to maintain is spreading weight evenly. Keep all of the load secured properly to the material.
3. To ensure optimal performance of these equipment, implement a routine maintenance plan. It will not only improve the efficiency of these machines, but also extend their operational lifespan, Maintenance activities should be scheduled and consistently carried out. This schedule can be based on different parameters such as the hours of operation, the load handled, or even the environment where the equipment is operated. A regular maintenance schedule helps to ensure that critical cleaning and inspection routines are followed, minimising the risk of unexpected equipment failure.
4. The operator in charge of material handling equipment should be well-versed with its functionalities. But only knowing this much isn’t enough. The operator should also have specific training on topics such as load distribution and handling techniques, maintenance protocols and safety training.
5. Moving heavy objects across the plant floor can be tricky. So, always plan these movements. While these movements are taking place, keep the floor clear to avoid any mishaps. Analyse the layout of the facility to ensure efficient material flow. Implement technologies such as conveyor systems, automated guided vehicles (AGVs), or robotics to streamline the movement of materials.
6. Safety should be a top priority when operating such equipment. Ensure the use of personal protective equipment (PPE) by operators and enforce strict adherence to safety protocols. Regularly inspect equipment for any potential hazards and address them promptly. Otherwise, some unnoticed malfunction in the equipment can lead to serious accidents. Provide clear signage, floor markings and training on safe equipment operation to prevent accidents.
By following these best practices for material handling equipment in India, an organisation can improve its competitive edge, improve customer satisfaction, and create a positive and productive work environment.