FAQs on MRO and their answers
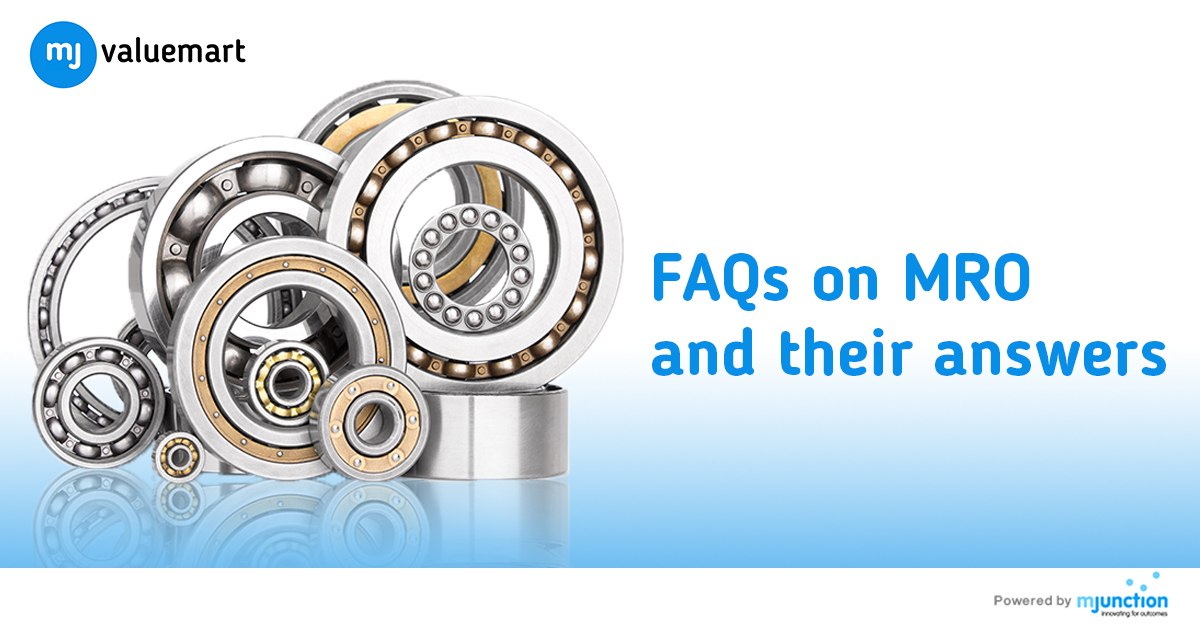
Companies across industries need a stock of MRO spares parts to keep their businesses running smoothly. MRO is connected to the upkeep of a facility, including running of the daily operations and maintenance of the facility. A significant investment goes in maintaining the MRO inventory and its management. As one of the leading e-marketplaces for genuine and unused MRO spares, we answer some of the FAQs on MRO:
What is MRO?
Answer: MRO stands for Maintenance, Repair and Operations. MRO is a vast term that encompasses all the processes and activities associated with maintenance of equipment that produce the main business output as well as electrical and plumbing systems that support the main business operations.
What is the difference between direct and indirect spend on MRO?
Answer: Direct expenditure refers to the money spent on procuring goods and materials to help in driving profit performance. Indirect expenditure includes money that is spent on goods and services that are needed for day-to-day operations but do not directly contribute to a company's bottom line.
What are the different types of MRO spares?
Answer: Though all types of MRO spares are used for running the facility, they are categorised into four different types.
- Infrastructure repair and maintenance: This includes maintenance of the building and its surrounding areas such as roofs, doors, windows, parking lots, electrical systems and plumbing.
- Production equipment repair and maintenance: These MRO spares are directly involved in the production process. The inventory of this type of MRO spares need to be carefully managed to avoid unscheduled downtime. This type of MRO spares could include ball bearings, gear boxes and shafts.
- Material handling equipment maintenance: This covers all the equipment required to move raw material to the production line and finished products to the loading docks. This includes maintenance of material handling equipment such as hand pallet trucks, stackers, hydraulic floor cranes and conveyors.
- Tooling and consumables: Drills, drivers, wrenches, socket sets and bits are some of the common tools used in manufacturing facilities. Gloves, goggles, safety glasses, face shields and PPE are all examples of consumables.
Why is MRO management important?
Answer: Businesses needed proper MRO stock to keep their facilities, systems and assets and equipment up and running. MRO inventory management is important so that employees have the access to the right tools at the right time. Mismanagement related to MRO spares can result in avoidable loss of man-hours and downtime.
How to achieve MRO efficiency?
Answer: There are various ways in which you can improve MRO efficiency and some of them are:
- Organise inventory
- Perform regular audit
- Forecast demand
- Buy and sell inventory strategically
Looking to buy or sell MRO spare parts?
mjvaluemart.com is a multi-vendor e-marketplace that connects the sellers with the right buyers across the country. You will find MRO spares such as ball bearing housing, ball bearing rollers, gear boxes and fasteners on the online platform. Sellers and buyers can directly negotiate the price. While buyers can buy unused MRO spares at a discounted price, sellers get better realisation for the MRO spares. To become a buyer, register here.