Useful insights on emergency response and machine spare parts safety
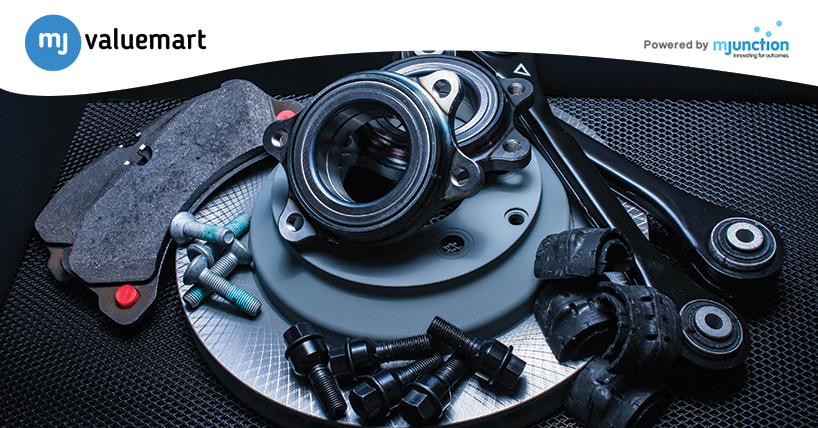
Emergency response and spare parts safety are important areas to address. By having a well-defined emergency plan and ensuring safety in managing machine spare parts, organisations can effectively respond to crises and minimise risks. Here we discuss some of the useful insights on emergency response and machine spare parts safety:
1. Maintain an up-to-date inventory of critical spare parts necessary for the operation and maintenance of equipment or machinery. Identify the most essential parts and ensure an adequate supply is readily available. To improve spare part efficiency, implementing a robust and straightforward work order process is important. Develop a streamlined work order process that is not overly complex yet ensures the transmission of necessary information. If the process is overly complicated, employees may deviate from the desired process, leading to inventory inaccuracies.
2. Conduct a risk assessment to identify potential risks or events that may impact the availability or usability of spare parts. Consider factors such as supplier reliability, lead times, transportation disruptions, natural disasters, or unexpected increases in demand.
3. Maintaining comprehensive documentation is important for emergency response. This documentation should include details such as specifications, part numbers, suppliers' contact information, and lead times for each spare part. A well-prepared document can help you quickly identify the required spare parts during emergencies and expedite the procurement process.
4. Define clear procedures for responding to spare parts-related emergencies. This includes steps to activate the emergency response team, initiate communication with suppliers, assess available stock, explore alternative solutions, and expedite the delivery or repair process.
5. Buy from reliable suppliers. This selection process should involve conducting a thorough evaluation of suppliers' manufacturing processes, quality control measures, and their track record in delivering high-quality spare parts. By scrutinising these aspects, you can confidently partner with suppliers who prioritise quality and have a proven reputation for consistently providing high-quality spare parts. If you are planning to buy machine spare parts online, explore mjvaluemart. We are an e-marketplace for genuine, inspected, and unused MRO spare parts.
6. Upon receipt, the spare parts must undergo a meticulous inspection process to verify their adherence to the required specifications. During inspection, various factors such as dimensions, material quality, and other relevant parameters must be looked at.
7. Provide comprehensive education and training to employees regarding the risks associated with moving parts. By raising awareness and offering proper guidance, you can help your employees to identify potential dangers, take necessary precautions, and maintain a safe working environment.
8. It is important to thoroughly examine the condition, functionality, and integrity of spare parts to prevent safety risks or failures.
9. Regular lubrication of spare parts helps to create a protective layer between moving components, reducing friction and wear. This preventive measure not only extends the lifespan of the spare parts but also contributes to the overall smooth operation of the equipment.
10. Proper storage of spare parts is important to prevent degradation or damage. This includes maintaining appropriate environmental conditions, including temperature, humidity, and other relevant factors.
By integrating these tips into operational frameworks, you can create safer work environments, optimise productivity, and enhance overall resilience in the face of emergencies and spare parts management challenges.