Bearing Lubrication: Useful Insights to Check
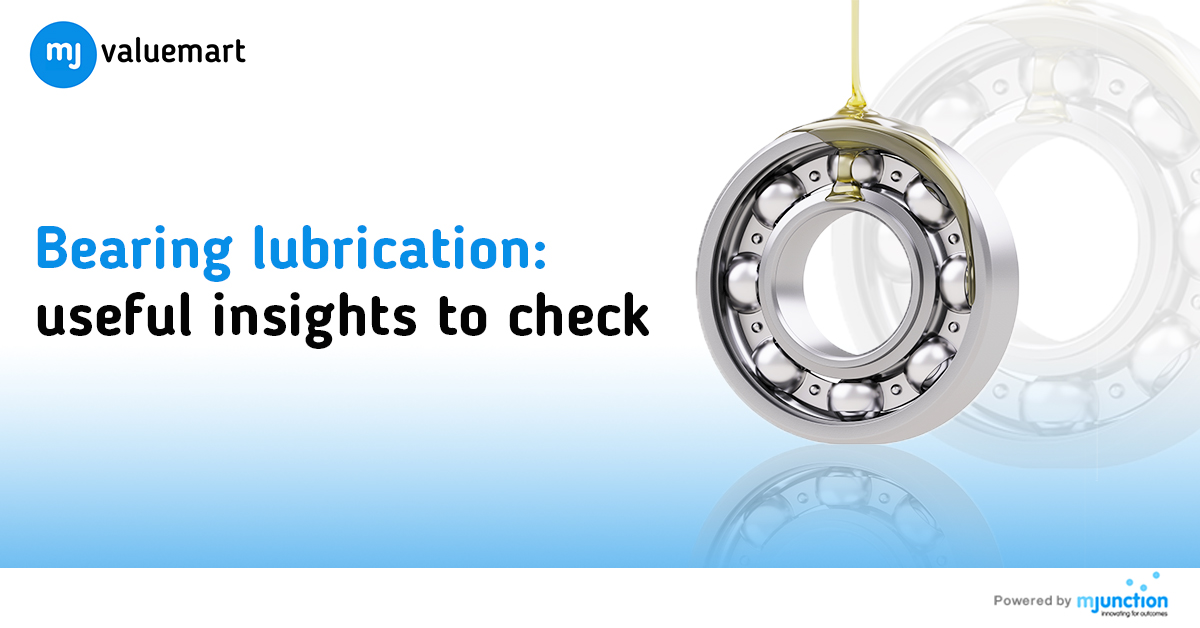
Regular lubrication improves the performance and lifespan of bearings. It reduces friction between the internal sliding surfaces of the bearing components and reduces metal-to-metal contact of the rolling elements with their raceways.
Some of the benefits of lubricating bearings are:
- Protecting surfaces from corrosion
- Sealing against contaminants
- Creating a barrier between rolling contact & sliding surfaces
- Providing heat transference
Here we share with you some useful insights on bearing lubrication:
Types of lubricants: There are two basic types of bearing lubricants: oil and grease. The choice of lubricants depend on various factors which include the type of machine, bearing type, size, temperature, load, speed range, operating conditions and external environment. The oil and grease have their own benefits.
- Oil: Oil lubricants are commonly used in high speed and high-temperature applications where it is necessary to transfer heat away from the bearings.
- Grease: Grease is the most common lubricant used for bearings. Unlike oil, grease doesn’t leak.
Note: The best way to select the right lubricant is to follow the bearing manufacturer's recommendations.
Lubrication methods: There are many different methods used for applying oils and grease on bearings. Common methods are:
- Oil drip feed lubrication: In this method, drip feed oilers are mounted directly on lubrication points. These oilers dispense oil through needle valves. They are used in systems where low loads and low-to-moderate speeds are expected, as bearings of this type require small quantities of oil that are applied at regular intervals.
- Oil splash feed lubrication: The bearings are spattered with oil by moving parts that are regularly passed through an oil-filled trough. This method helps in reducing bearing operating temperature and is ideal for applications with high speed and temperature.
- Forced feed systems: In a forced feed system, an oil pump circulates lubricating oil to all the bearings. This kind of system needs boiler feed pumps, compressors, gearboxes and turbine generators.
- Grease lubrication: Grease is applied with special lubricating equipment that deposits the grease between the balls forcing them into, and around, the raceway. When the balls or rollers rotate the grease gets distributed within the bearing.
Why lubrication is important: Proper lubrication has a direct effect on the bearing life. Most bearing failures are related to lubrication and contamination issues.
- Loss of lubricant: When bearings are not greased at regular intervals, it can contribute to equipment failure.
- Incorrect grease: Not all bearings are compatible with all lubricants. Use of inappropriate lubricants can not only affect the efficacy of the equipment but also reduce its lifespan.
- Excess lubrication: Excessive lubrication is not good for the equipment. Excessive lubrication can cause the rotating bearing elements to overheat. This results in increased wear and tear.
Proper application of lubricants: Besides choosing the right lubricant and appropriate lubrication method, it is important to remove any existing oils, anti-corrosion coatings and greases. This step is essential in eliminating any potential incompatibilities. The second most important thing is that the right quantity of lubricant should be used. To know the proper fill quantity refer to the manufacturer’s manual.
Looking for bearings for your business? Buy unused, genuine MRO spares from mjvaluemart
Buy large volumes of unused, genuine MRO spares such as self-aligning ball bearing, needle roller bearing and taper bearing.We connect you with the sellers with excess unused inventory of MRO spares. Buyers can log in to check unused products available at competitive prices, place the products online and get them delivered to their doorstep. To become a registered partner, submit your request.